Tuesday, February 11, 2014
One Down One To Go
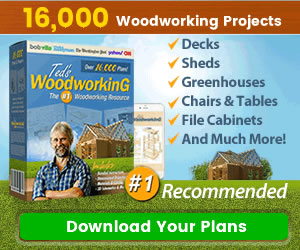

I ended up laying a total of six coats of amber shellac on this block of wood sanding in between the first couple with 220 grit and between the remaining with 320. I left it a couple of days to set and then I had a good look at it. I wasnt so happy. It had great colour, the finish was even, but it lacked depth and had way too many brush marks. I decided to just sand the hell out of it, starting with 220, moving to 320 and finishing with fine steel wool. I figured if I sanded through the finish it didnt matter as I was going to have to lay on more coats anyway. While I didnt end up sanding through the finish, I did cause some serious differences in the colour.
While I was working away on this I got an email from a friend who had viewed the last post and he wanted information about applying shellac. I told him it was easy, forgiving and fast drying, all the things guys like us want in a finishing product, among other things. He mentioned how he had bought a French Polish kit from Lee Valley, but after reading the instructions, he though it was probably too difficult. Now theres a word that makes me sit up and take notice, "difficult".
Back on line I read about four or five articles about this process and he was right, it did sound difficult, not to mention time consuming. From what I gathered, building up the finish was the worst part of the process, but hey, I already had one didnt I? Out came the shellac and rags. I didnt have the suggested type of alcohol, but they said it was what Rubbing Alcohol that is used to clean monitors is made from, and I sure had some of that. I mixed up a batch; two parts shellac to one part rubbing alcohol, made myself a paddle from a rag and went to work. Wow. Incredible finish. The rag allows you to get it on evenly and without brush marks. The finish was beyond belief, so I was sold. I rubbed on three or four coats, let it dry, and I was ready for the final run.
Have you ever noticed that the smaller the job, the more Murphys law kicks in. Im sure it is because we get cocky - hey, its a small job, right? No big deal.
The next day I rubbed the entire block down with extra fine steel wool and Minwax Finishing Wax. I laid that stuff on like it was a buck a gallon, rubbing, laying on more wax and rubbing some more. I let it sit up for about a half hour and then, with a couple of the softest rags I could find, I started polishing. As I polished off the first bit of wax this incredibly bright, deep, highly glossed surface came through. It absolutely blew me away.
Once the wax was buffed I had an objective look. I shouldnt have done that, but looking at things objectively forces you to face your mistakes. I should have corrected that difference in colour before I continued on with my faux French Polish job. The colour difference was still there, but doubled. The finish was smooth, man, was it smooth. The surface was shiny, but the colour was blotchy and inconsistent. And therein lies the lesson - believe what the book tells you.
The shot at the top shows the rubbed out finish. You can see the differences in colour, especially on the right side and along the front bead. The three vertical faces, however, were even and smooth so I went with it. Its a drill index after all, and the top is just going to get drilled with a whole bunch of holes.
Once, when my son was visiting and we were checking out the tool cabinet, he said that when I was done, anyone will be able to follow the process of the build just by viewing the quality of the different pieces. The first piece I put the beading plane to was a disaster, but they eventually got better the more I did. My first set of hand-cut dovetails looks more like sloppy finger joints, but over time, they improved too. So now, when someone looks at this thing in the future, they will be able to say, "...and here is where he started to learn French Polishing".

I went with the finish and covered the entire thing with masking tape. There is three reasons for this. First, I would like to be able to complete the piece and put it into the cabinet finished before I smack it with something and bugger the finish. I figured if covering it with masking tape works on American Chopper when they are assembling a bike, it will work here too. The second reason for taping is to help minimize tear-out when I start to drill all those holes. Finally, the third reason is that I have to tape the template to the top for drilling and I want to completely cover the top with good, old carpet tape so the template will be held down flat and smooth. I love carpet tape and use it for almost everything, but it has one drawback - it really reaps havoc with the finish. Stick something down to a finished surface with carpet tape and you can bet when you lift it off, the surface will come with it. By covering the surface with the easy release, 5 day, green 3M tape, I wont have that problem.

This is the template I made up about seven months ago. I put it together in Illustrator, an Adobe vector program that I find just perfect for this type of thing. I just made a document slightly larger than the actual size of the block, then started making circles with cross-hairs in the middle, one for every bit that was to go in the index. It took a day of playing with positioning and alignment, but it worked out very well. Printed off on 11 x 17 stock, I just cut it down to fit the top of the block and taped it down. I was ready to drill.

So here is the finished product. The block has four feet made with a 3/4 inch tenon cutter. I drilled into the bottom of the block with a 3/4 inch Fostner bit, glued the dowels into them then set it on a piece of 80 grit sandpaper that was stuck to the glass plate I use for lapping my blades. After a few minutes of that, the block didnt rock and was stable, but more importantly, it had airspace beneath it for circulation.
Drilling the holes took me two afternoons, about eight hours in total. The eleven largest brad bits have a shoulder that I wanted the hole to follow so that was twenty-two goes just for them. The twists were straight shafts, so they were not quite as much work.
Originally I thought I would drill the hole with the same sized bit that the hole was to hold, then pour some water down it, let it sit to swell the wood, vacuum it out and then re-drill the hole so when it dried, it would be slightly larger. Ya, I know, sounds like a lot of work doesnt it? Surprisingly though, all of these holes were drilled with the same sized bit as the bit the hole holds, and drilled only once I might add. While it was a hassle to load a bit, drill one hole, then start the process over again, it really wasnt that bad. The only bits that didnt like their same sized hole were the ones smaller than 5/16th. All of these smaller holes had to be reamed twice with a little "giggle" to the block during the second reaming. Once drilled I coated the inside with wax to give some sealing to the inside walls of the hole. There is a lot of holes in it and they are pretty much aligned with each other and all are 1 3/4 inches deep leaving only a 1/4 inch at the bottom to hold together. I still have to make an index card for it, showing a numbered layout of the bits with a list of sizes below it.
This piece sits on a shelf on one of the doors of the cabinet. I have to do something to keep it in place when I open and close the door and that is where the round feet come in. I plan to make a female piece to match the front feet and fix those to the shelf. This is the reason for the flush ring handle - to lift the front of the block up out of those holders and bring it forward so I can grab it and lift it out.
I have no idea how long this thing will last as I could wake up tomorrow to find it split down the middle. Overall, I am very happy with the results. I finally no longer have to dig for a needed bit in those frustrating metal boxes. As with everything in this cabinet, the next one will be better.
One down - one to go...
Peace,
Mitchell
Subscribe to:
Post Comments (Atom)
No comments:
Post a Comment